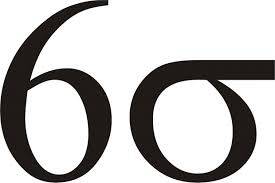
In today's dynamic and competitive business landscape, organizations are continually seeking ways to optimize their operations and enhance performance. Operational excellence, characterized by efficient processes, minimal waste, and high-quality outputs, has emerged as a cornerstone of business success. To achieve operational excellence, companies are increasingly turning to methodologies such as Lean Six Sigma, which integrate principles of Lean manufacturing and Six Sigma quality management. This paper delves into the concept of operational excellence and explores how the adoption of Lean Six Sigma practices can drive organizational effectiveness and competitiveness.
Literature Review
Definition of Operational Excellence
Operational excellence refers to the relentless pursuit of efficiency, quality, and customer satisfaction through the continuous improvement of processes and systems (George, 2002). It involves optimizing every aspect of operations, from resource allocation to workflow design, to deliver superior value to customers while minimizing costs and waste.
Lean Six Sigma Methodology
Lean Six Sigma is a hybrid approach that combines the Lean principles of waste reduction and process efficiency with the statistical tools and techniques of Six Sigma for quality improvement (George, 2003). While Lean focuses on eliminating non-value-added activities and maximizing flow, Six Sigma aims to identify and reduce variation in processes to achieve near-perfect quality.
Benefits of Lean Six Sigma Implementation
Research indicates that organizations implementing Lean Six Sigma initiatives experience a wide range of benefits, including increased productivity, reduced lead times, enhanced product quality, and greater customer satisfaction (Pande et al., 2014). By systematically identifying and eliminating process inefficiencies and defects, companies can realize significant cost savings and competitive advantages.
Challenges in Implementing Lean Six Sigma
Despite its potential benefits, implementing Lean Six Sigma is not without challenges. Common barriers include resistance to change, lack of leadership support, inadequate training, and difficulty sustaining improvements over time (Snee & Hoerl, 2003). Successful deployment requires a holistic approach that addresses cultural, organizational, and technical factors.
Case Study Analysis
To illustrate the practical application of Lean Six Sigma principles in achieving operational excellence, we present a case study of Company XYZ, a leading manufacturer in the automotive industry. Facing increased competition and customer demands for higher-quality products, Company XYZ embarked on a Lean Six Sigma initiative to streamline its production processes and improve overall efficiency.
Through a series of cross-functional teams and Kaizen events, Company XYZ identified key areas for improvement, such as reducing cycle times, eliminating defects, and optimizing inventory management. By leveraging Lean tools such as value stream mapping and 5S workplace organization, the company was able to identify and eliminate waste in its operations, resulting in significant cost savings and improved productivity.
Furthermore, by implementing Six Sigma methodologies such as DMAIC (Define, Measure, Analyze, Improve, Control), Company XYZ was able to systematically analyze process data, identify root causes of defects, and implement targeted solutions to improve quality and reliability. As a result of these efforts, Company XYZ achieved a 30% reduction in defects, a 20% increase in productivity, and a 15% improvement in on-time delivery performance within the first year of implementation.
Discussion and Conclusion
The case study of Company XYZ highlights the transformative impact of Lean Six Sigma principles on achieving operational excellence in business. By adopting a systematic approach to process improvement and engaging employees at all levels, organizations can drive significant performance gains and gain a competitive edge in the marketplace. However, successful implementation requires strong leadership commitment, effective change management, and a culture of continuous improvement.
In conclusion, the integration of Lean Six Sigma principles offers a powerful framework for organizations seeking to achieve operational excellence and sustain competitive advantage in today's fast-paced business environment. By focusing on eliminating waste, reducing variation, and delivering value to customers, companies can position themselves for long-term success and growth.
References
George, M. L. (2002). Lean Six Sigma: Combining Six Sigma quality with lean speed. McGraw-Hill.
George, M. L. (2003). Lean Six Sigma for service: How to use Lean Speed and Six Sigma Quality to Improve Services and Transactions. McGraw-Hill.
Pande, P. S., Neuman, R. P., & Cavanagh, R. R. (2014). The Six Sigma way team fieldbook: An implementation guide for project improvement teams. McGraw-Hill Education.
Snee, R. D., & Hoerl, R. W. (2003). Leading Six Sigma: A step-by-step guide based on experience with GE and other Six Sigma companies. FT Press.