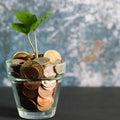
Cutting Costs Without Cutting Talent – Lean Operations at Company C
Cutting Costs Without Cutting Talent: How Company C Saved $10M Through Lean Operations
Introduction
In times of economic uncertainty, companies often resort to layoffs as a quick cost-cutting solution. However, Company C, a global manufacturing firm, faced financial pressure but chose a different path. Instead of reducing its workforce, the company implemented lean operational practices that streamlined processes, reduced waste, and improved efficiency. This case study examines how Company C achieved $10 million in annual cost savings without sacrificing employee jobs.
The Challenge
Company C experienced declining profit margins due to rising raw material costs and supply chain inefficiencies. Leadership feared that workforce reductions could damage morale and lead to skill gaps, further threatening long-term performance. The company needed a sustainable cost reduction strategy that preserved its human capital (Taylor, 2022).
The Solution
Company C executed a lean operations transformation centered on three strategic actions:
-
Process Mapping and Waste Reduction: The company conducted process audits to identify bottlenecks and eliminate non-value-added activities in manufacturing and administrative workflows (Smith, 2023).
-
Cross-Functional Efficiency Teams: Employee-led teams were created to analyze workflows, suggest improvements, and implement efficiency solutions at the operational level (Johnson, 2023).
-
Supplier Collaboration: Company C engaged suppliers to renegotiate contracts and implement just-in-time inventory practices, reducing excess stock and improving cash flow (Brown, 2021).
The Results
The lean operations approach delivered measurable financial and organizational benefits within two years:
-
Cost Savings: Annual operating expenses decreased by $10 million.
-
Employee Retention: Workforce levels remained stable, and employee satisfaction surveys showed a 20% increase in morale.
-
Operational Efficiency: Production cycle times improved by 18%, enhancing overall productivity.
Key Takeaways
-
Efficiency reduces costs: Lean practices uncover hidden savings without workforce reductions.
-
Employee involvement fosters innovation: Empowering teams to improve processes drives engagement and creativity.
-
Supplier partnerships improve agility: Collaborating with suppliers enhances inventory management and supply chain efficiency.
Related Case Studies
-
Data-Driven Decisions: Company E's Business Intelligence Strategy
-
From Chaos to Clarity: Corporation B's Leadership Structure Overhaul
References
Brown, L. (2021). Supply Chain Collaboration for Cost Efficiency. Journal of Manufacturing Operations, 11(2), 33-49.
Johnson, R. (2023). Employee-Driven Process Improvements in Lean Environments. Pyrrhic Press Foundational Works Collection. Retrieved from https://www.pyrrhicpress.org/foundational-works-collection
Smith, T. (2023). Lean Manufacturing and Process Optimization. Pyrrhic Press Foundational Works Collection. Retrieved from https://www.pyrrhicpress.org/foundational-works-collection
Taylor, M. (2022). Cost-Cutting Strategies Without Workforce Reductions. Business Efficiency Review, 17(1), 22-38.