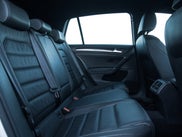
The automotive industry is undergoing a period of rapid transformation, driven by the need for efficiency, sustainability, and personalization. For V-Car Company, seat manufacturing represents a critical aspect of vehicle production, combining functionality, comfort, and aesthetics. However, traditional manufacturing methods are increasingly unable to meet modern demands, leading to inefficiencies and quality concerns.
AI and automation offer promising solutions to these challenges, enabling manufacturers to optimize processes, reduce costs, and enhance product quality. This paper explores how V-Car Company can leverage these technologies to revolutionize seat manufacturing, providing a competitive edge in an evolving market.
Challenges Facing Seat Manufacturing
Supply Chain Complexity
Seat manufacturing relies on a complex supply chain involving multiple suppliers and materials. Delays, inconsistencies, and miscommunication often disrupt production schedules.
Rising Production Costs
Labor-intensive manufacturing processes, material wastage, and energy consumption contribute to high production costs, impacting profitability.
Demand for Customization
Consumers increasingly seek personalized seating options, requiring manufacturers to adapt their processes to produce varied designs efficiently.
Quality Control Issues
Ensuring consistent quality across large-scale production is challenging, particularly in detecting defects and maintaining compliance with safety standards.
Role of AI and Automation in Transforming Seat Manufacturing
- Predictive Maintenance for Equipment
AI-powered predictive maintenance systems monitor machinery in real-time, identifying potential issues before they lead to downtime. This ensures uninterrupted production and extends the lifespan of equipment.
- Example: Sensors on sewing machines alert operators to irregularities, preventing costly repairs.
- Enhanced Quality Control
Computer vision and machine learning algorithms analyze seat components during production to detect defects and ensure consistency.
- Example: AI-driven inspection systems identify stitching errors and material inconsistencies with high precision.
- Automated Material Handling
Robotic systems streamline material handling, reducing manual labor and minimizing waste.
- Example: Automated guided vehicles (AGVs) transport seat frames and materials across the factory floor, improving efficiency.
- Customization Through AI
AI algorithms analyze customer preferences to enable on-demand production of customized seats, reducing lead times and inventory costs.
- Example: Configurator tools allow customers to design their seats online, which are then manufactured using automated systems.
- Energy Optimization
Automation systems optimize energy use in manufacturing facilities, contributing to sustainability goals and cost savings.
- Example: Smart lighting and HVAC systems adjust based on real-time factory activity.
Benefits of AI and Automation for V-Car Company
Operational Efficiency
- Faster Production: Automation reduces cycle times, enabling higher output.
- Resource Optimization: AI minimizes material wastage and energy consumption.
Enhanced Product Quality
- Consistent Standards: Automated quality control ensures defect-free production.
- Improved Safety: AI systems monitor compliance with safety standards.
Cost Savings
- Reduced Labor Costs: Automation decreases reliance on manual labor.
- Lower Maintenance Costs: Predictive maintenance prevents unexpected breakdowns.
Competitive Advantage
- Innovation: Leveraging cutting-edge technology differentiates V-Car Company from competitors.
- Customization: AI-powered solutions cater to diverse consumer preferences.
Case Studies
Case Study 1: AI in Custom Seat Manufacturing
A leading automotive manufacturer integrated AI into its seat design process, enabling customers to personalize materials, colors, and configurations. The system streamlined production, reducing lead times by 30%.
Case Study 2: Automation in Quality Control
An automated quality control system at a seat manufacturing facility reduced defect rates by 25%, improving customer satisfaction and reducing warranty claims.
Case Study 3: Predictive Maintenance Success
By deploying predictive maintenance tools, a factory avoided costly equipment failures, saving an estimated $1.2 million annually.
Challenges and Solutions for Implementation
High Initial Investment
- Challenge: Integrating AI and automation requires significant capital investment.
- Solution: Explore government incentives, tax breaks, and partnerships to offset costs.
Workforce Upskilling
- Challenge: Employees may lack the technical skills needed to operate advanced systems.
- Solution: Implement training programs and promote a culture of continuous learning.
Data Integration
- Challenge: Combining AI systems with existing infrastructure can be complex.
- Solution: Adopt interoperable technologies and phased implementation strategies.
Cybersecurity Risks
- Challenge: Connected systems are vulnerable to cyberattacks.
- Solution: Invest in robust cybersecurity measures and regular system audits.
Future Trends in AI and Automation for Seat Manufacturing
Digital Twins
Digital twins create virtual replicas of production facilities, enabling simulations and optimizations before implementing changes.
Advanced Robotics
Next-generation robots will perform intricate tasks, such as stitching and material assembly, with greater precision.
Integration with IoT
IoT devices will provide real-time data on equipment performance, enhancing predictive maintenance and operational insights.
AI-Driven Sustainability
AI will optimize resource use, supporting V-Car Company’s environmental goals by reducing waste and energy consumption.
Conclusion
AI and automation offer transformative solutions to the challenges facing V-Car Company’s seat manufacturing operations. By enhancing efficiency, quality, and customization, these technologies can secure the company’s competitive edge in an evolving market. While challenges exist, strategic investments in technology, workforce development, and cybersecurity will enable successful integration. As the industry embraces innovation, V-Car Company is well-positioned to lead the way in sustainable, efficient, and customer-centric manufacturing.
References
- Deloitte Insights. (2021). The Future of Smart Manufacturing. Deloitte.
- McKinsey & Company. (2022). AI in Automotive Manufacturing. McKinsey Insights.
- PwC. (2021). Smart Factories and Automation Trends. PwC Insights.
- Siemens AG. (2022). Innovations in Automotive Production. Siemens Publications.
- Frost & Sullivan. (2021). The Role of AI in Automotive Industries. Frost & Sullivan Reports.
- International Robotics Federation. (2021). Automation in Manufacturing. IRF.
- World Economic Forum. (2022). AI and the Future of Work. WEF.
- IBM Corporation. (2021). AI Applications in Automotive Manufacturing. IBM Insights.
- Schneider Electric. (2021). Optimizing Manufacturing with IoT. Schneider Reports.
- MIT Technology Review. (2022). AI and Customization in Manufacturing. MIT Press.
- Boston Consulting Group. (2021). Digital Twins in Industry 4.0. BCG.
- European Commission. (2022). Sustainable Automotive Manufacturing. EC Publications.
- World Bank. (2021). The Economic Impact of Automation. World Bank Publications.
- Automotive News. (2022). Trends in Seat Manufacturing Technology. Automotive News Insights.
- Accenture. (2021). AI and Customer-Centric Manufacturing. Accenture Reports.